电子硬件产品制造指南(四):组装测试及包装发货


版权声明
我们非常重视原创文章,为尊重知识产权并避免潜在的版权问题,我们在此提供文章的摘要供您初步了解。如果您想要查阅更为详尽的内容,访问作者的公众号页面获取完整文章。

电子硬件产品制造指南摘要
本系列制造指南专为中批量生产的电子硬件产品设计,涉及基础生产任务与不同产量下的生产方式差异。电子产品的产量划分标准有多种,而不同规模的生产商对“小批量”定义可能不同。在讨论产品产量时,应确保有共同的标准。
卫Sir提醒,在安排生产前需确定产品数量。小批量生产推荐200以内,随着产量增加,考虑使用自动化技术提升效率,降低人工成本。PCBA的复杂性也会影响自动化程度。
1 - 大批量生产
大批量生产注重自动化和库存控制。供应链管理变得关键,以确保最小库存同时避免生产中断。设计师、开发者与供应链负责人需保持沟通,以降低成本、提高质量或应对元件短缺。小批量中的手工作业可能转向自动化,且设计阶段需考虑减少手工作业。
2 - 小批量生产
小批量生产关注固定成本降低,这通常意味着更多手工操作。建议简化库存控制,保持较多元件库存以减少风险。"停产前购买"策略可避免零件短缺。飞针测试代替传统针床测试,以提高测试效率。
包装是销售前的最后工序,通常由人工完成,包装简化有助减少失误。设计与开发注重创造力,而制造文化强调流程管理和重复性。工厂与设计师/开发者可能在变更管理方面存在分歧。
设计师/开发者在办公室或实验室设计的产品,需由生产负责人确保高效、可靠的生产。对小变动,如更换电容,设计师可能视为小事,但对工厂意味着程序更改、测试和物料管理等一系列操作。
合理的沟通和理解对于确保生产工作的顺利进行至关重要。
祝 好
产品人卫朋

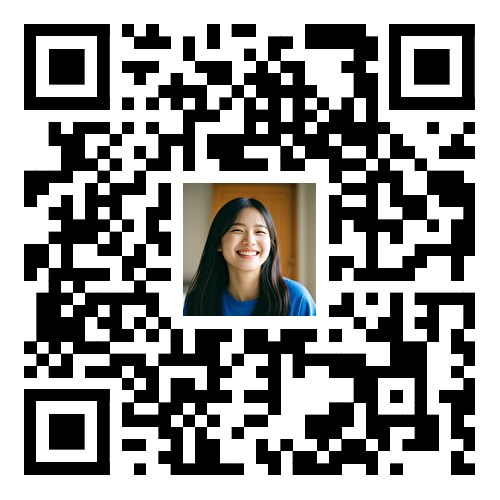
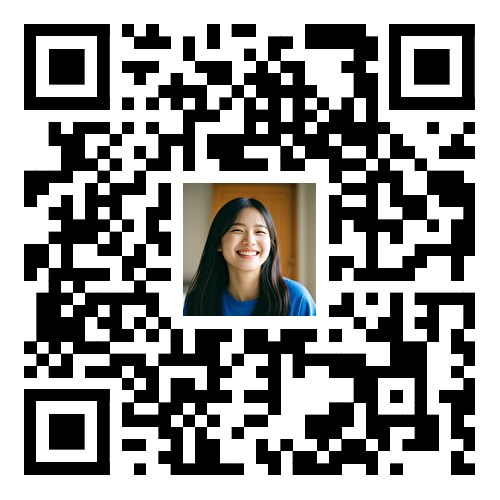
白皮书上线