质量管理体系五大工具概述

我们非常重视原创文章,为尊重知识产权并避免潜在的版权问题,我们在此提供文章的摘要供您初步了解。如果您想要查阅更为详尽的内容,访问作者的公众号页面获取完整文章。


质量管理体系及其五大工具摘要
质量管理体系是提高汽车行业质量管理水平和竞争力的关键,其中五大核心工具包括APQP、SPC、MSA、FMEA和PPAP。这些工具已超出汽车行业的应用范围,成为质量工程师必备的技能。这套方法是预防为主,旨在设计和制造过程早期防止潜在错误,构成IATF 16949标准的基础。
IATF 16949是在ISO 9001基础上为汽车行业定制的质量管理要求,专用于汽车行业供应链中的生产制造环节。
五大质量工具
APQP 是一种从项目立项到PPAP结束的质量计划和项目开发计划,旨在减少供应商产品质量策划的复杂性,并确保产品满足客户需求。
SPC 利用统计技术监控过程并确保产品服务符合要求,已成为六西格玛和精益制造的关键部分。
MSA 评估测量系统精度,确保测量系统的变差尽可能小,以提高测量精度和可靠性。
FMEA 是一种分析产品设计和过程设计中潜在失效模式及其后果的系统化方法,提高产品质量和可靠性。
PPAP 确定供应商是否理解顾客要求,并证明生产过程能够满足这些要求,是APQP的一个环节,确保产品一致性和可靠性。
这些工具不仅覆盖了新产品的研发到投产、量产控制的整个过程,也延伸到整个供应链中,成为联系项目开发与量产批准的关键环节。
本文内容参考了多个网上文献,在此表示感谢。
想要了解更多内容?


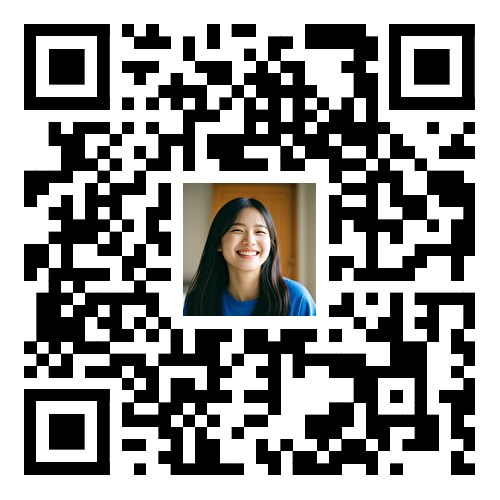
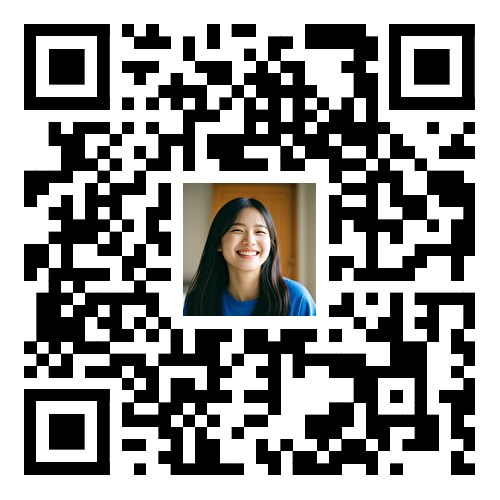
白皮书上线